産業用ロボットの知能化は「経済安全保障上も重要」Mujin滝野氏が目指す究極の目標
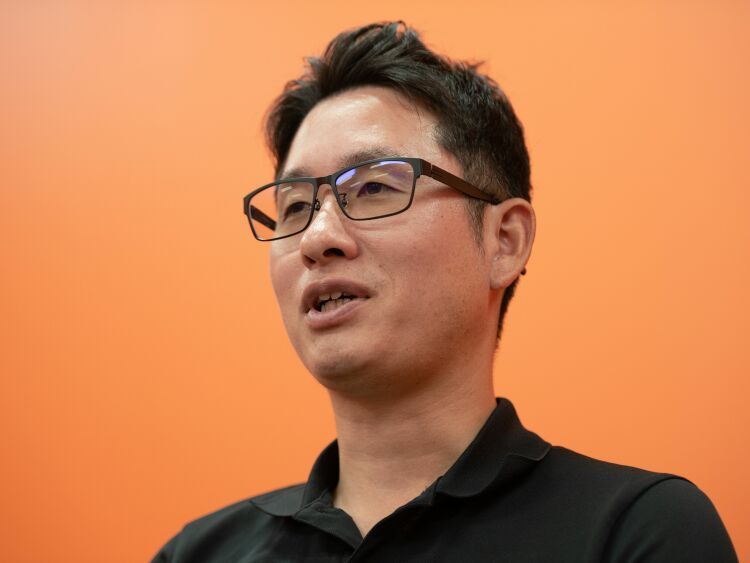
――日本の産業用ロボットは世界の半分ほどのシェアを占め、各メーカーが高いレベルでしのぎを削っています。そんな中、御社の製品は注目を集めています。
言うまでもなく、日本の産業用ロボットのブランド力はすごくて、いずれも完成度は高いわけですが、まだまだ自動化されていない部分があります。当社はそこをターゲットにしています。
そのために必要なことは、ロボットを単に自動化するのではなく、「知能化」することです。当社がやっているのはそういうことです。
産業用ロボットの多くは、教えたことを繰り返すことはできます。ハードウェア(機械)としてね。ただ、そのためには、ロボットを現場に導入する前に、「ティーチング」という設定作業が必要です。電源を入れればすぐに自動的に動くという代物ではないんですね。
ティーチングとは、ロボットの動きを一つひとつプログラミングしていく作業であり、そのために必要な担当者の技術や熟練度は相当高いものが求められます。
仮にティーチングがうまくいったとしても、そもそも従来のロボットは同じ動作を繰り返すことはできても、臨機応変な対応は難しかったのです。
例えば「ばらばらに積まれたものを取って置く」という作業などはハードルが高かった。なぜなら、商品の種類が多く、かつそれらが置かれた位置や姿勢が一様ではないからです。それらあらゆるケースを想定してロボットに動きをティーチングするのは不可能でした。
当社はまず、こうした課題を克服するために「Mujinコントローラ」というものを開発しました。小さな箱形の装置なのですが、言ってみればロボットの頭脳に当たる機器です。これを既存のロボットに取り付ければ、そのロボットが「知能化」され、最適な動きを自立的にやるようになります。ティーチングも必要ありません。
――魔法のようなコントローラーですが、仕組みはどうなっているのでしょう。
Mujinコントローラには、ロボットを知能化するためのソフトウェアが搭載されているのです。それを支えているのは、センシングと独自開発した機械知能の技術です。
仕組みとしては、3Dビジョンカメラで物体の位置や姿勢、さらには周辺環境を正確に認識します。その上でロボットの最適な動作経路を瞬時に計算し、ロボットの自立的な動作を生成します。
そのコア技術の一つはモーションプランニングです。自動運転にも採用されていて、ロボットの最初と最後の行動や姿勢を指示するだけで、あとは状況に応じてロボットが作業するようになります。
――コントローラーを取り付けることで既存のロボットが「知能化」できるのであれば、企業にとってもコストパフォーマンスは大きいですね。
おっしゃる通りです。もちろん、ロボット自体がすごく旧式の場合は難しいですが、ここ数年のものであれば取り付けることができます。
ただ、そうやって既存のロボットを活用する以外にも、要望があれば当社の自動化機器類を活用いただくことも可能です。
ロボットに関わる自動化機器類自体も弊社製であれば、いわゆる「ブラックボックス」がないんですよね。トラブルが起きたとき、他社製だとロボットや各種機器の内部の状況などがすぐにわからず、何が原因なのかを突き止めるのにどうしても時間がかかってしまう。その結果、生産ラインや物流ラインの停止時間が長引くこともあります。
ロボットが導入されている現場は基本、大量の商品を扱っています。10分、1時間、あるいは1日稼働を停止したら、かなりの損害になるわけですね。
ところで、今お話ししたのはロボット単体の知能化についてですが、当社が実現したのはそこにとどまりません。
――と言いますと?
工場や倉庫には複数のロボットが稼働していますよね。アームで商品を取って箱の中に入れるロボットや、運搬を担当するロボット、掃除機のような台車型のAGV(Automatic Guided Vehicle)という搬送ロボットなど。
当社の技術では、それら一つひとつを知能化ソフトウェアで制御することで、生産ラインや物流ラインの規模で、全体の作業がスムーズに進むようすべての自動化機器類の制御をインテグレーション(統合)することができます。
生産ラインや物流ラインで、今一体何が起きているのかという情報もリアルタイムでわかりますし、それは現場にいなくてもリモートで確認できます。
様々なデータも取れるので、それを分析して現場の改善に役立てたり、次の商品開発に活用したりもできます。出荷量が増えればそれだけデータが蓄積されるので、データドリブンな改善や経営判断が可能になります。
データの活用方法はほかにもあって、日々の稼働状況がこれだけ「可視化」されると、在庫をどれだけ持てばいいのか、物流や生産ラインの稼働具合などについて、予測精度が高まるんですね。
最近、ERP(=Enterprise Resources Planning)ソフトがはやってますよね。企業全体の最適化を図るため、生産や調達、在庫、販売、財務、人事などといった企業の経営資源を一元管理できるソフトです。
これまでだと社長は各部門の状況について、それぞれの担当役員にいちいち聞かなくてはならなかったんですよね。ところがERPの仕組みを導入すると、トップが直接、リアルタイムで日々の動きを確認できるんです。そうするとコストダウンするにしても、在庫管理するにしても迅速な判断ができます。
ところが肝心の現場でDXが遅れてデータが取れていなければ、ERPの仕組みに組み込むことができません。その意味でも、当社が提供しているサービスや商品はとても親和性があると思っています。
産業用ロボットを扱っているので一見、ハードウェアの会社に見られがちです。もちろん一部のハードウェアも作っているのですが、最大の強みはロボットの頭脳にあたるソフトウェアの開発力、制御技術です。その意味では当社はソフトウェアよりの会社です。
やっぱりこのぐらいのレベルまで自動化されないと、今人間がやっている仕事をロボットがこなすことはできないんですね。単純な仕事というのはすでに日本のロボットメーカーは自動化していて、あと残っている領域はこうしたレベルの話だと思います。
――人間が今やっている仕事をできるだけ自動化するということですが、社名のMujinは日本語の「無人」から取っていますよね。自動化と関係がありますか?
おっしゃる通り、社名は当社のビジョンと関係しています。それは、人を単純作業や過酷な労働から解放し、生活や社会を豊かにするための時間に充てて欲しいという思いです。当社の自動化ソリューションやサービスによって、工場や倉庫から一切の人がいなくなり、無人になることが究極の目標です。
自動化のメリットは「働き方改革」の点だけではありません。企業側、経営者側にとってもメリットがあります。例えば欧米では、最近のインフレにより、工場や倉庫で働く人たちの時給が上昇しています。一般的なアルバイトでさえ、時給30ドルを超えていると聞きます。今の為替ですと、日本円で4700円ぐらいです。だからといって、企業は消費者に届ける製品の値段を一気に1.5倍とかにはできないわけです。
一方で、労働力不足が深刻な国もあります。そこでも賃金は高くなります。
国の経済安全保障や地政学的なリスクの観点からも自動化は注目されると思います。欧米各国はかつて、人件費が安いからとこぞって中国に工場を建てて商品を生産していました。
しかし、人に頼る生産現場では何が起きるかというと、ノウハウの流出です。作り方、品質管理の仕方、出荷や物流のあり方などを教えるのには時間がかかるのですが、そこでせっかく育てた人材を丸ごと引き抜かれてしまうと、致命的な損失になりかねません。
生産ラインや物流システムを自動化してしまえば、そういったリスクは減ります。生産ラインや物流を「回す」というノウハウは流出するかもしれませんが、どうやって生産するのかという、メーカーにとって最も重要なものは守られます。
技術を守るということは人件費を抑えること以上に重要でしょうから、その意味でも自動化に対するニーズは今後、世界的に増えていくと思います。
――生産ラインや物流ラインなど、各社によって違いはあるでしょうし、まして業種が異なればがらりと現場は変わる気がするのですが、そういう状況でも対応できるのでしょうか。
当然、我々としてもノウハウがたくさん蓄積している業種や現場はありますが、導入事例がない現場だからといって、断ることがないようにしています。というのも、そういう現場でもチャレンジすることで、今後のノウハウとして蓄積されるからです。
我々が不慣れな現場というのは、お客様にとってもこれまであまり自動化を進めたことがないというケースが多いんですね。なので、お客様と一緒に取り組んでいくという感じですね。
――競合他社はいるのですか。
同じようなことをしている会社は当然あります。その中でも最も古くからやっているのが当社であり、10年以上に渡って積み上げてきたノウハウというのはそんなにすぐ追いつかれるものではないと思います。
その理由の一つに制御の問題があります。すでに述べたとおり、産業用ロボットはソフトウェアとハードウェアの両方にまたがる製品です。ハードウェアが正しく動くように、ソフトウェアで計算して、予測して制御していくわけですが、いざ実際に動かそうとすると、どうしても想定通りにいかないこともあります。
ここで重要になってくるのが、現場との「すり合わせ」です。うまくいかなかったとき、現場から取得できる状況や情報をパラメーターにして、それをプログラムに加味していくと。ただ、状況や情報は無数にあるので、その中からどれをパラメーターとして加えるかは、これまで培ってきたノウハウがものを言います。
テクノロジーだけならGoogleなど、世の中にはすぐれた企業はたくさんあるでしょう。それでもこの業界になかなか進出できないのは、今言ったようなソフトウェアとハードウェア、そして現場まで熟知することが相当ハードルが高いからだと思います。
――話題は変わります。滝野さんはなぜこの業界に入られたのですか。最初の就職もアメリカだったと聞きました。
両親がいずれも海外志向で、特に母親の友人が海外にいたので、母親について子どもの頃から海外旅行に行くことはよくありました。加えて母親は英語の先生だったので、その影響もあって僕自身、英語の勉強は結構やっていました。そんなことがあって、アメリカの大学に進学しました。
大学在学中、大学の財務や寄付などを担当していた証券会社出身の方と知り合いになり、財務諸表の読み方など金融や企業財務について教えてもらったんです。それがきっかけで投資にも興味を持ち、投資家のウォーレン・バフェットさんが好きになりました。
大学卒業後、就職したのはイスラエルの切削(せっさく)メーカー「イスカル」でした。日本ではあまり知られていないかもしれませんが、隙間市場で高いシェアを誇る、いわゆるニッチトップの企業で、バフェットさん率いる投資会社が完全子会社化したんですね。それで入社を決めました。
この会社で営業担当として働いていた頃、Mujinを一緒に創業したデアンコウ・ロセンと出会いました。ロセンは当時、ロボットの研究や開発を手がけるアメリカの企業にいて、2009年に日本であった国際ロボット展に出席するため、来日していました。
ビジネスにおける私の師匠的な立場の人がたまたまこの会社にいたので、僕も休みを取って展示会の手伝いをしていたんです。そこでロセンと出会い、それからというもの、彼からメールや電話で起業の誘いを受け続けたんです。最初は断っていたのですが熱意にほだされて、その2年後、会社を辞めてMujinを一緒に設立しました。
――昨年はシリーズC(黒字経営が安定した段階における資金調達)総額150億円の資金調達を達成しました。ソフトウェアの会社だ、と言いながらハードウェアとしてのロボットも自社開発していますね。当初からこうした事業展開を見越していたのですか。
我々が創業したときのビジョンというは、世の中にたくさんある単調な仕事とか危険な仕事などを自動化して、人間には人間にしかできない仕事に時間を使ってもらい、それによって生産性を上げてもらいましょうというものでした。
これは現時点まで変わっていなくて、このビジョンを達成するためにどうしたらいいんだと突き詰めていった結果、産業用ロボットとなり、ロボット単体では実現できないからセンサーだと。さらには搬送系のロボットも必要だからやろうかと。お客様の要望に応えるべく開発やサービス、商品も展開してきたという感じなんですよね。
お客様にとっての価値は何か、本来求められているゴールは何かというところをぶれずに追求したら、自然とここまでやらないとだめだよねという感じで、少しずつ大きくなっていきました。