まるで大木のミノムシ ロープだけで風力発電の点検、人呼んで「ニンジャ・テック」
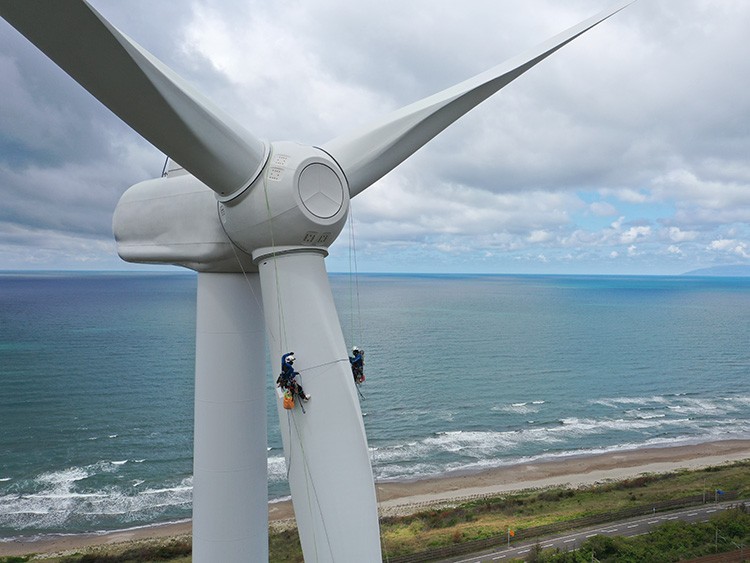
まるで大木の枝にぶら下がるミノムシのようだ。秋田県由利本荘市の日本海を望む高台に立つ日立造船の「岩城勝手風力発電所」。連休明けの5月、特殊高所技術の3人が風車の点検・補修作業をしていた。地上80メートルの高さからロープをおりながら、ブレード(羽根)に落雷などによる損傷がないかチェックしていく。
特殊高所技術で風力発電事業を担当する美濃輪茂樹さん(48)は「足場などを使わずロープでぶら下がって上下左右に移動する独自技術で、海外では『ニンジャ・テック』と呼ばれている」と説明する。
2007年に設立した同社は、高速道路の橋梁やダムなど高いところでの作業を担っていたが、10年に風力発電設備のメンテナンス事業に参入した。ドイツの風車メーカーから「ロープで作業ができる人を欧州から送り込むとお金がかかる」という理由で依頼された。当時、風車でロープ作業ができるのは国内では同社だけだったからだ。クレーンを使って足場を設置すれば費用が数千万円規模になってしまうこともあるが、同社の場合は数百万円程度。ただ、当時は風力発電のメンテナンスの重要性が認識されておらず、それほど依頼は多くなかった。
状況が変化したのは、東日本大震災後だった。同社は関西電力などから揚水発電のメンテナンスを依頼されていた。コンクリートにひび割れがないかなどを点検する仕事で、作業のためにダムを2週間程度止める必要がある。ところが、東京電力福島第一原発の事故を受け、全国の原発が止まって電力不足が懸念され、揚水発電がフル稼働したため止めて点検することができなくなった。
一方、風力発電の仕事は増え始めた。震災直後の11年、経済産業省が福島県沖で始め、復興のシンボルとして注目が集まった浮体式洋上風力発電の実証研究事業。日立製作所製の出力2メガワットと5メガ、三菱重工製の7メガの計3基の風車のメンテナンスを担った。7メガの風車は海面からブレードの先端まで200メートル近くあり、当時世界最大級だった。
さらに、新エネルギー・産業技術総合開発機構(NEDO)が千葉県銚子市沖と北九州市沖で進めていた着床式洋上風力発電の実証研究事業で、三菱重工製と日本製鋼所製の風車の作業もおこない、その後はNEDOによる北九州市沖の浮体式洋上風力のメンテナンスも受注した。国内にある洋上風力発電のほぼすべてで作業したことになる。
もちろん洋上ではクレーン車を使えず、200メートルに及ぶような高さのクレーン船を使えば億単位のお金がかかりかねない。特殊高所技術は日本の大手メーカー3社すべての風車のメンテナンスを担っているが、3社が相次いで自社生産から撤退してしまった。
美濃輪さんは「メーカーによってブレードの材質や補修の仕方が異なるので、海外メーカーの研修を受ける手続きを進めている」という。洋上風力に強い欧州のヴェスタスやシーメンス・ガメサ、米ゼネラル・エレクトリック(GE)といった大手メーカーを検討している。
経産省は17年から風力発電設備の定期安全管理審査制度を始めたが、いまブレードのメンテナンス作業ができる業者は限られる。需要は右肩上がりで、売り上げ全体の3割超を占めるまでに成長した。
同社は技術者54人を抱えるが、風力の担当は21人ほど。3人1組で作業し、風が強いと作業できないため1カ所2週間ほどかかることもある。メンテナンスは風車を止めて作業するため、風が比較的弱くなる5月から10月にかけてするのが一般的だ。年間40~50基のメンテナンスを請け負っているが、これから建設が増えていけば手が足りなくなる。美濃輪さんは「風車は20年間稼働するが、風が強い東北地方の日本海側は落雷が多く発生する。人材不足のまま新しい大型風車がどんどん建っていって大丈夫だろうか」と話す。