3Dプリンターが開く持続可能性の未来 産業廃棄物もCO2も大幅削減
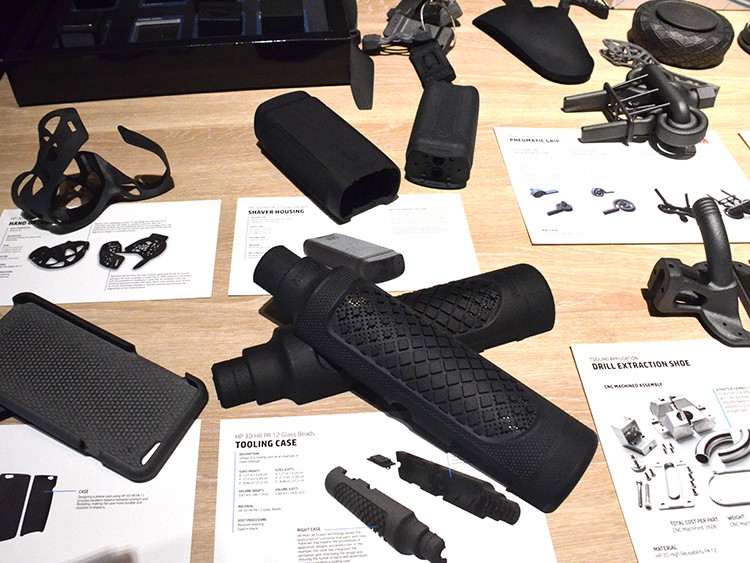
例えばかつて家庭の必需品だった「ラジカセ」。既に生産が終了した製品もあるが、今も学校などで広く使われており、ときどき「ハンドルが壊れた」と修理や部品交換の依頼がある。
製品の生産終了後も一定期間、補修用部品は保存しているが、メーカーにとって、いつ注文が入るか分からない部品を保管するコストは意外に大きい。倉庫に保管するスペースや、管理のための人員が必要だ。部品を製造する金型も場所を取る。金型は放置するとさびるので定期的にメンテナンスする。そのための人員を確保し、トレーニングもしなければならない。
3Dプリンターで必要な部品を必要な数だけ生産できれば、金型も、保管スペースも要らなくなる。音響機器メーカーのJVCケンウッドと、3Dプリンターを製造・販売する日本HPは、ラジカセなどのハンドル部分を3Dプリンターで製造し供給できないか、技術的な検討を進めている。
オーストラリアの医療ベンチャーが販売している、扁平足の矯正用インソール。複雑な形状のため、これまではプラスチックの大きな塊から1個1個削りだして作っており、プラスチックの削りかすが大量に発生していた。
しかし3Dプリンターで直接製造するようになってからは、1足あたり約1.4キロ発生していた産業廃棄物が5グラム以下に減ったという。
3Dプリンターは1980年代に開発され、2010年代に普及が進んで話題になった。複雑で細かい形状の立体を、組み立てや切断工程を経ずに作れる。
しかしナイロン樹脂を何層にも重ねて吹き付けるため、素材の向きによって強度が大幅に異なり、素材の強度に限界があった。工業製品への応用では、試作モデルの制作が主流で、最終製品への利用には不向きとされていた。
既存のプリンターではトップメーカーの日本HPだが、3Dプリンターに参入したのは2016年と新しい。同社は、完成段階で各層をまとめて溶かし合わせる独自の技術を開発。ナイロン樹脂にガラス粉末を加えた素材も取り入れ、完成品の強度を大幅に高めて用途を大幅に広げることに成功した。
「最初からものづくりに使ってもらえる品質を目指し、技術開発に長期間を要した」と、同社の秋山仁・3Dプリンティング事業部長は話す。
同社は自社製品や工場の生産用部品に、3Dプリンターで作った部品を積極的に導入している。アジア太平洋・日本地域を統括するシンガポールで保管していた同社製品の部品の一部を3Dプリンターでの生産に置き換え、保管や輸送費用など数千万円のコスト削減につなげたという。
「3Dプリンターでできることは限りなく広がっているが、まだまだ、製品の正しい価値が認識されていない」と秋山氏。「3Dプリンターは、各社が目指している、ものづくりの変革にマッチするソリューションでもある。日本国内では職人的な気質で製造工程の改革が進んでいない業界もあり、潜在的な需要は大きいと考えている」と話している。