サプライチェーンの強化を進め 危機の時代にさらなる成長を
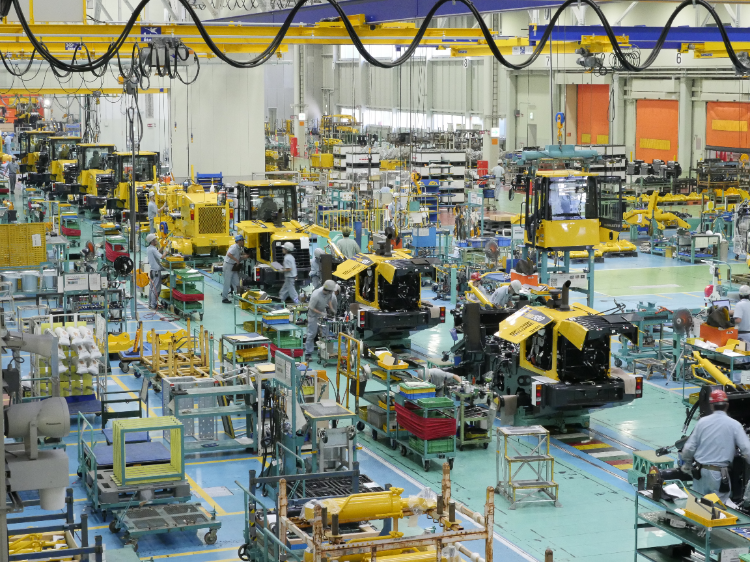
——コロナ禍で、コマツの生産・調達にも影響がありましたか。
当社は世界中にものづくりの拠点を85拠点持っています。そのうち海外は73拠点、生産金額ベースで50%を占め、そのなかでも比較的大きな拠点である中国で、港の閉鎖や工場の操業停止といった事態がまず起こりました。その後徐々に影響が欧州や東南アジアにも拡大し、一時は部品の調達で苦戦しましたが、コマツは従来、需要や為替の変動の影響を吸収するためグローバル調達として複数拠点からの調達に取り組んでいたこと、ある程度の在庫をサプライチェーン内に持っていたこともあり、コマツの国内の生産工場がストップするといった大きな影響は出ていません。今年になってからは、生産・調達ともに順調に推移しています。
――ただ、今後も何が起こるかわからない状態が続きます。
本当にそうですね。21世紀に入り世界は大きく変化し続けていますが、コロナ禍はその変化をさらに加速させたと思います。コマツ社内でも調達先を中国から東南アジアに移管できないかといった議論は続けていますが、自動車メーカー等に比べて我々の生産する建設機械というのはボリュームが非常に小さいので、調達力の面では劣勢にならざるを得ません。その分、ある程度の部品在庫を戦略的に確保するように努めたり、グローバルで補給部品等の在庫をコントロールすることなどで、自己防衛をはかっていこうと考えています。
――コマツはサプライチェーンのなかに協力企業の組織「コマツみどり会(以下「みどり会」)」を持っていることが特徴的ですね。
日本のほか、米州、欧州、中国、タイにも各拠点のみどり会があります。いずれも国内外にかかわらず優良な企業にはぜひ私たちの仲間になっていただきたい、ということで始まった活動です。昨年50周年を迎えた日本のみどり会は、当社の図面をもとに部品を製造していただくものづくり企業が約100社、タイヤやエアコン、ベアリングなどを当社に供給してくださる大手企業約50社で構成されています。
――こうした活動を行うメリットは何でしょう。
建設機械は需要のボラティリティーが非常に大きいので、多くのみどり会会員企業と得意分野を生かして協力し合うことで、フレキシビリティーを保てるというのが大きな理由です。もちろん、この部品はこの会社でなければ難しい、この精度は他ではなかなか出せないといった高い技術を持つ企業も多くおられます。また、みどり会では会員企業の経営者のなかには若い頃にコマツで研修を受けた経験のある方も多く、コマツではみどり会の2代目、3代目の若手経営者にコマツ社員と同様に働く経験をし、コマツの仕事の取り組み方を理解していただいています。また、コマツグループで実施する技能競技大会にも、みどり会から多くのご参加をいただいています。
――2019年に”第8回ものづくり日本大賞”で内閣総理大臣賞を受賞した「KOM-MICS」について教えてください。
これは製品と生産のプロセスデータを対応づけて蓄積することで、機械の止めない化・歩留まり向上・トレーサビリティーの確保、予知保全を実現するコマツ独自のIoT生産支援プラットフォームです。コマツでは20年ほど前から自動溶接ロボットを自社開発して使用していますが、その後の技術の進歩により、ロボットをネットワークにつないで様々なデータを取ることが可能になってきました。そしてそれができるのであれば、仕様がそれぞれ異なる工作機械でも同様のことができるのではないか、というのが発想の発端です。
私たちはまず、機械の動作のなかで「価値のある時間」と「価値のない時間」を分けて考えることから始めました。溶接ロボットであれば価値のある時間は金属を溶かして溶接している工程、工作機械なら切り粉を出して金属を削ったり穴を開けたりしている工程です。しかし実際には、その前後で人が準備をしたり、溶接するポイントを探したりするプロセスに時間をとられ、価値のない時間がずいぶんあることがわかりました。
――具体的には。
溶接ロボットの場合で、価値のある時間は工程全体の4割、工作機械で3割程度というのが私たちの解析結果です。正直、これには驚きました。それ以前からずいぶん効率化に努めてきたという自負があったからです。しかもコマツ全体で工作機械は4〜5千台あるため、すべてを一気に効率の良い機械に入れ替えるというわけにもいきません。まずは現有の設備を最大限活用するために、プログラムの書き換えや工具(機械の先端で実際に金属を加工する部分)の改良などに取り組み、現時点で価値のある時間を10%前後増やし、価値のない時間も10 ~15%ほど減らすことができています。
――現在もまだ発展中の技術ということですか。
もちろんこれで十分とは思っていません。KOM-MICSはメディアで「工場の見える化」を支援するツールと紹介されることが多く、機械の動きをモニターするシステムだけを指すと思っている方もいますが、私自身はみどり会などの協力企業を含む生産システム全体、あるいは生産計画にフィードバックすることで、サプライチェーンの最適化につながる広い概念と考えています。ものづくり大賞の受賞は大変光栄ですが、現時点での成果を評価されたというより、期待しているから頑張れという激励をいただいたものと思っています。
――あらためて、コマツの生産・調達の基本的なスタンスを教えてください。
車体本体の生産はできる限り需要の大きい地域で行う、というのが基本方針です。一方、エンジン、油圧機器、アクスル、電子機器などの高品質のキーコンポーネントは日本国内のみで開発・生産を行い、その他の部品はできるだけ多極生産することを基本としています。もちろんリスクヘッジ、価格競争力の強化が最大の目的ですが、先ほどお話ししたように自動車メーカー等に比べると調達力の弱い我々としては、優秀な現地のサプライヤーさんの成長を応援したいという思いも強くあります。
――そうした国内・国外の多くのサプライヤーに対して必ず共有してほしい価値観はありますか。
社内に対しても徹底するよう呼びかけているのは、価値判断の優先順位は「S(安全)・L(法令)・Q(品質)・D(納期)・C(コスト)」であるということです。建設機械の製造には多くの人手が必要ですので、なかなか労働災害を完全にゼロにはできていませんが、常にそこに向かっていくべきだと考えています。コマツでは調達本部のなかに生産現場の安全指導をサポートするチームを設け、みどり会をはじめとするサプライヤーのみなさんと一緒に安全活動に取り組んでいます。
――最後に、先の見えない時代にコマツがめざすこれからのビジョンをお聞かせ願います。
当社の社長の小川は、中期経営計画の活動として「モノとコトの両方でイノベーションを起こす」と繰り返し語っています。コマツの本質は手を動かし汗をかいてものづくりをする会社であり、それは今後も変わりませんが、ICTなど新しい技術も積極的に活用しながら「安全で生産性の高いスマートでクリーンな未来の現場」という当社のビジョンを実現していくことが最大の目標です。
コロナ禍はたしかに世界を変えつつありますが、当社においてはこれまでの自分たちの働き方を見直す契機にもなりました。むしろこの変化を、何かひとつでもプラスに変えるための出発点にする。そんな意識で向き合うことができれば、私たちの製品も変わり、お客様にさらなる価値を生むことができるのではないかと考えています。